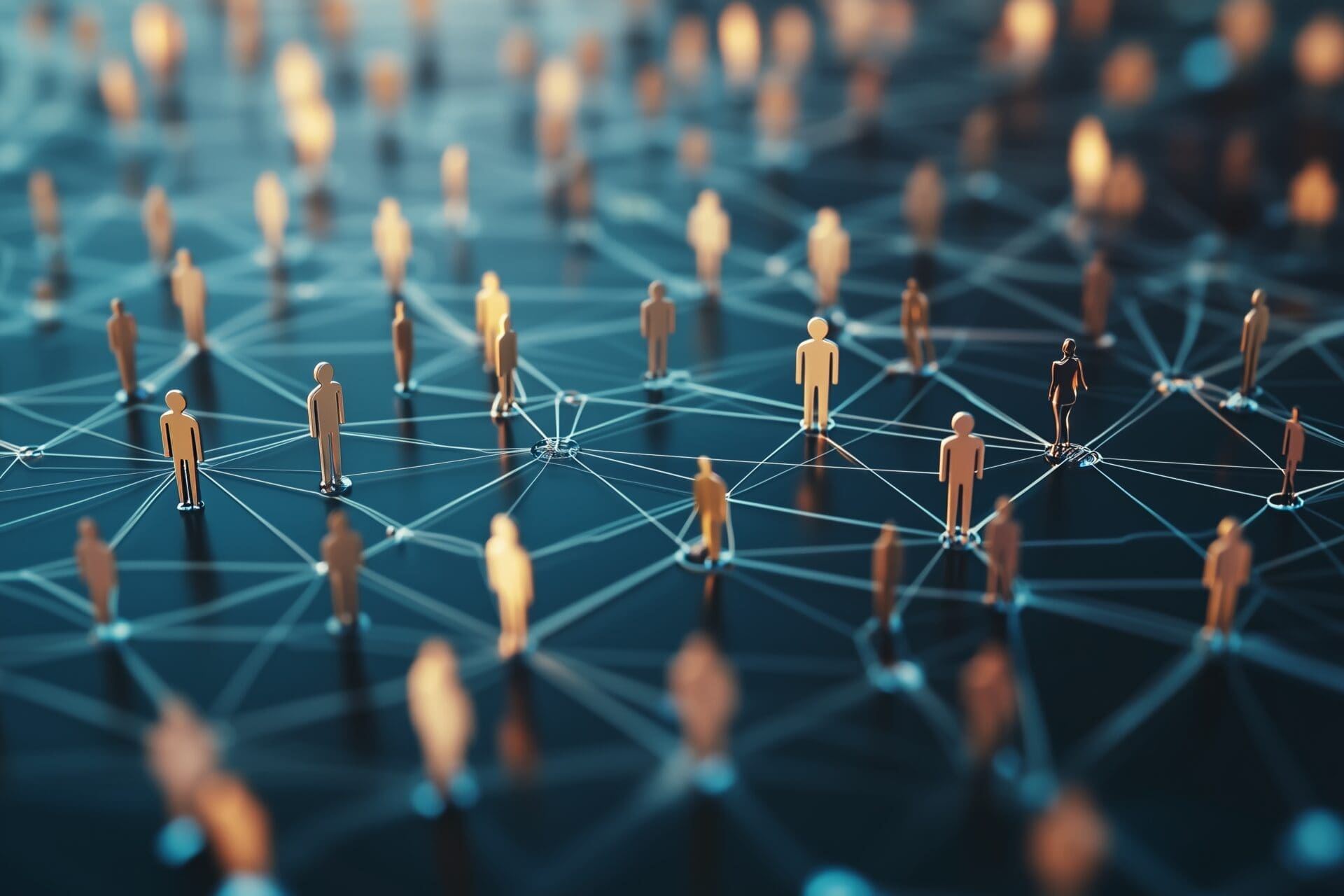
Organizational Structure
September 13, 2019
Simplify your HR processes with Lean Management: more accessible than you think
Are you struggling with bottlenecks that are wasting valuable time? Are your processes too cumbersome and causing you to lose efficiency? Has the quest for excellence added steps to your ways of doing things, to the detriment of organizational agility?
Lean Management may be the solution for you. Directly inspired by Lean Manufacturing methods, Lean Management comes to your office, sparing your administrative processes which deserve to be optimized.
The DMAIC approach applies very well in every company, regardless of its size or sector of activity. This approach consists of:
-
- D: Define the problem
- M: Measuring the performance gap
- A: Analyze performance gaps, errors, defects
- I: Implement the chosen solutions
- C: Control key variables to maintain the gains obtained
To help you, map out your process, which involves identifying each step one by one. On small pieces of paper stuck to the wall or in suitable software, you must create a detailed visual of your process. Don’t think you’re going into too much detail. Instead, be specific and segmented for each step. For example, an approval email represents a step, as does revising a document before sending it. Each task is a step in itself. Please note that it is only once all the steps are clearly identified that you will be able to eliminate them.
Once the non-value-added steps are identified and ready to be removed (Muda), focus on a faulty step that could be the source of the errors. Is it a task that is too difficult or excessive (Muri), or is it an environment with too many irregularities and fluctuations to guarantee convincing results (Mura)?
To facilitate the search for waste that may be the source of your lack of efficiency, Taïchi Ohno, founding father of the Toyota Production System, has identified the most widespread waste: overproduction, overstocking or unnecessary stocks, unnecessary transport and travel. ,overprocessingor unnecessary processing, unnecessary movements, errors, defects and rejects, waiting times and delays, underutilization of skills.
Do you recognize yourself? This is completely normal. Continuous improvement is an infinite process. And now that you are aware of the possible solutions, we bet that you will have to take action!
Need a helping hand? We can support you in your process.

Julie Tardif, CPHR
Chief Commercial Officer, Co‑Founder & Partner
Speaker & Certified Trainer
Human Resources Consultant
Advice Centre
Discover more inspiring content
Find out how our methodology has transformed companies from different sectors. Each article is proof of our expertise.
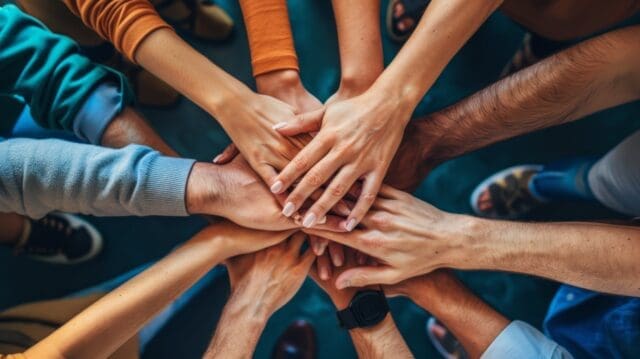
Culture and Health Wellness
PsyCap – This commitment lever that has an impact
PsyCap is a crucial mindset influencing employee engagement. Employers can strengthen this capital to encourage engagement. (147 characters)
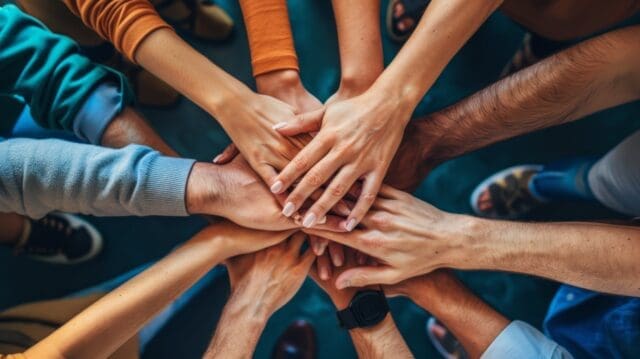
Culture and Health Wellness
The company released to mobilize 96% of your employees
Companies are adapting to the VICA era by adopting the concept of liberated enterprise, based on trust and employee empowerment.
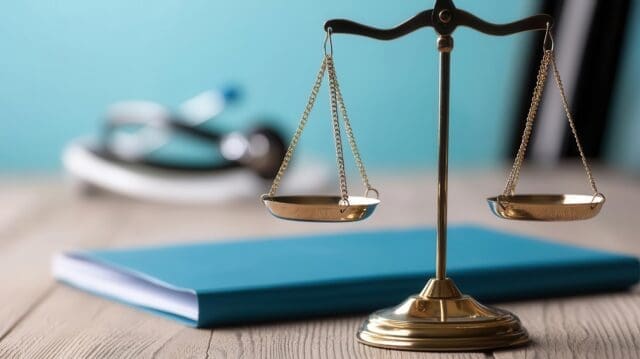
Overall Compensation
Time is a paid remuneration
HR Advisor responds to the challenge of attracting talent in SMEs: offering time, an effective and profitable alternative.
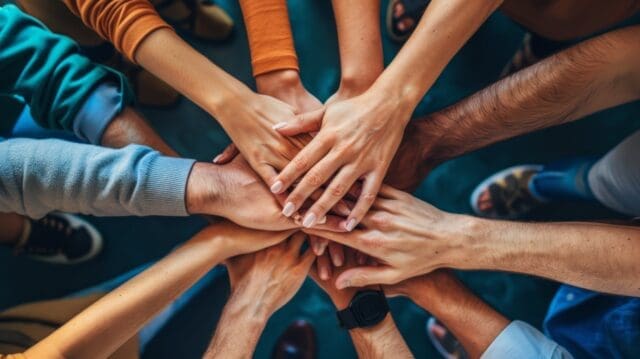
Culture and Health Wellness
The antidote for a culture of innovation: overcoming the fear of failure
A culture of innovation is essential to stand out. We must value creativity, accept failure and encourage employee engagement.
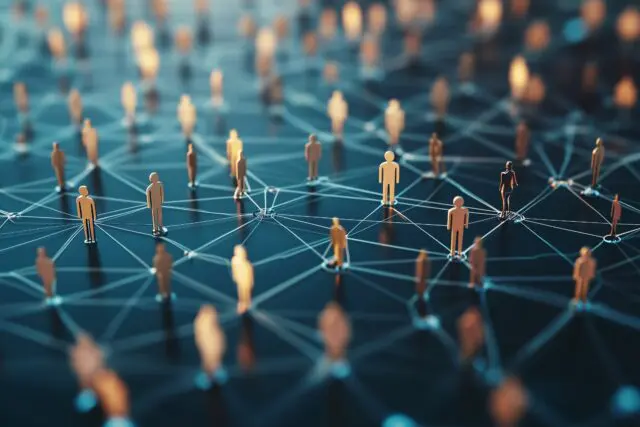
Organizational Structure
What if you listened to your HR advisor?
Human resources management integrated into company strategy. Strategic HR advisor to improve competitiveness, productivity and loyalty.
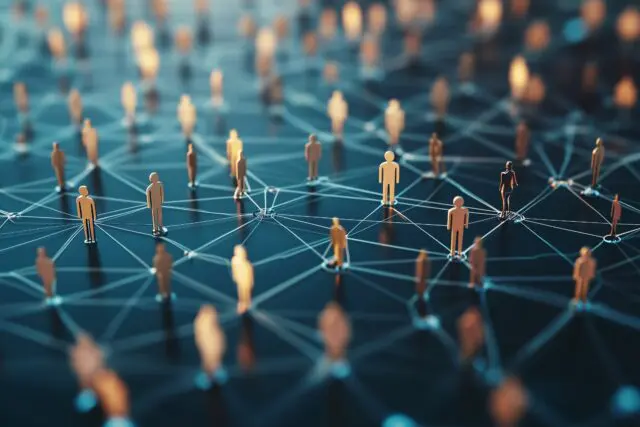
Organizational Structure
Your HR practices can also be tech!
Companies must adapt to the digital shift by improving the candidate experience through the integration of new technologies.
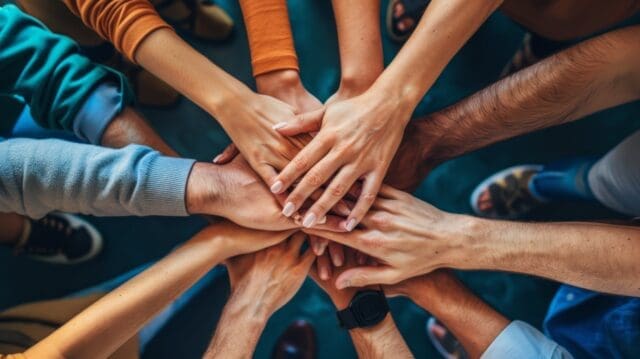
Culture and Health Wellness
Get around the labor shortage by better retaining your employees
To counter the labor shortage, retain your employees through continuing training and skills development for your managers.
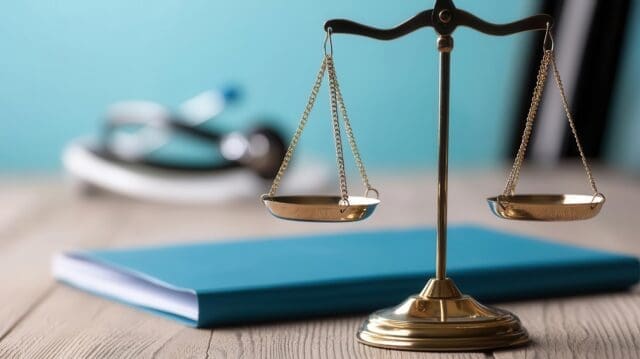
Overall Compensation
No salary increase for two years…
Maintain employee trust by increasing two-way communication and transparency. Measure performance and reward it fairly.
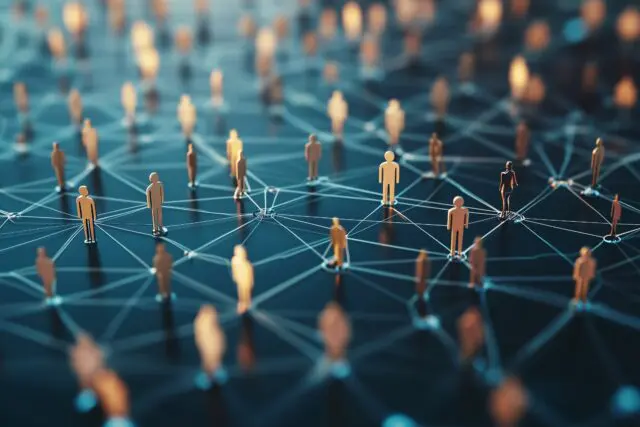
Organizational Structure
Innovation or failure?
SMEs are hesitant to invest in HR technologies due to fear of failure and resistance to change, thus hampering their organizational culture.

Employee Coaching & Training
Imposter syndrome: a danger for businesses
Impostor syndrome affects managers’ self-esteem and confidence. It can be prevented by assessments and coaching.
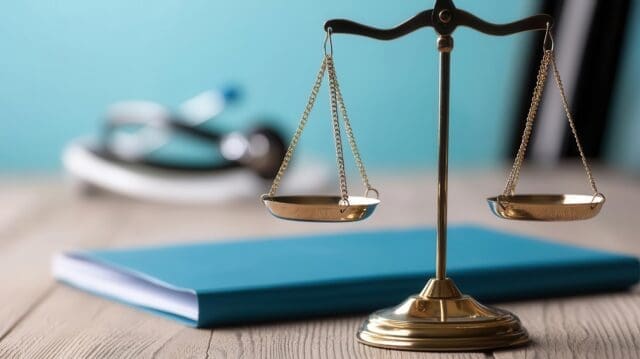
Overall Compensation
When remuneration becomes creative: wow effect guaranteed!
Leaders must innovate to attract talent. Creative compensation packages, such as vacation subsidy, are popular.
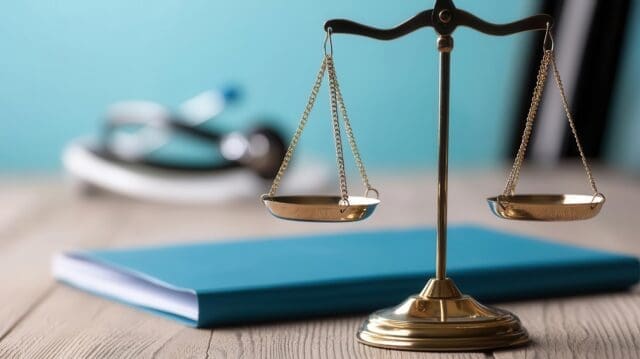
Overall Compensation
Wage pressure: what to do?
Attract and retain talent: offering attractive overall compensation, including non-monetary benefits, is essential in the face of salary pressure.